Methods Analysis
Charting
Learning Objectives:
- Explore common types of charts used in methods analysis, including flowcharts, process maps, time-motion charts, Gantt charts, Pareto charts, histograms, and scatter plots.
- Understand the characteristics, applications, and limitations of each type of chart and when to use them based on the nature of the data and the objectives of analysis.
A Process Chart is a graphic means of representing the activities that occur during a manufacturing or servicing job. There are several types of process charts. These can be divided into two groups.
Those which are used to record a process sequence (i.e. series of events in the order in which they occur) but do not depict the events to time scale. Charts falling in this group are:
Operation process chart
Flow process chart – (man / material / equipment type)
Operator chart (also called Two Handed Process Chart)
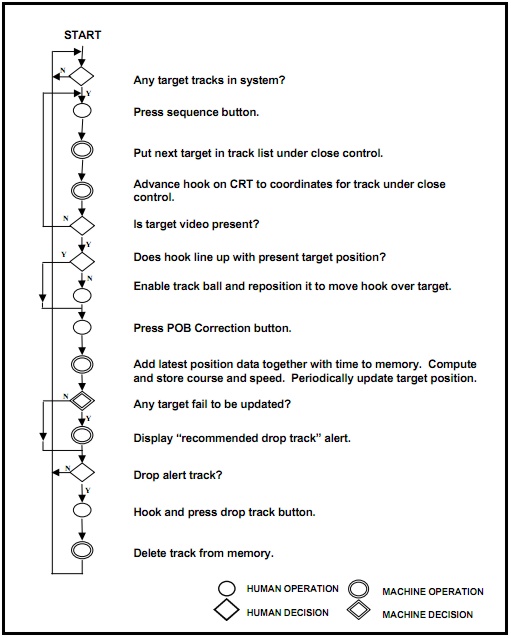
faa.gov, Public domain, via Wikimedia Commons
Solved Example: 9056-01
A bar chart is drawn for:
A. Time versus activity
B. Activity versus resources
C. Resources versus progress
D. Progress versus time
Correct Answer: A
Solved Example: 9056-02
Pareto Chart is used to:
A. Identify the critical factor caused for the defect
B. Average number of defects in production
C. Demonstrate the frequency distribution of good quality production
D. Express the bar chart for mathematical analysis
Correct Answer: D
Solved Example: 9056-03
Control charts for the attribute are concerned with:
A. Checking if the variable is out of control
B. The actual measurement of the parameter, comparing with a standard
C. Qualitative checking of defects
D. Direct measurement of the variable for control
Correct Answer: C
Solved Example: 9056-04
R charts are control charts for:
A. Variables
B. Reliability
C. Attributes
D. Maintainability
Correct Answer: A
Solved Example: 9056-05
Bar chart is suitable for:
A. Large project
B. Major work
C. Minor work
D. All of these
Correct Answer: C
Workstation Design
Learning Objectives:
- Define workstation design and its importance in optimizing work processes, productivity, and ergonomics.
- Explain how effective workstation design contributes to worker comfort, safety, and overall efficiency.
- Describe the principles of ergonomics and human factors that are essential for workstation design.
- Understand how ergonomic design can minimize the risk of injuries, reduce worker fatigue, and enhance overall well-being.
- Approach of ergonomics is to consider product dimensions in human terms in view of constraints placed on the design by body size variability. Eg. Seats
- Information about body size in not directly applicable to a design problem.
- Designer has to analyze in what ways anthropometric mismatches are possible and then decide on which data might be appropriate to the problem.
- Designer has to develop clear ideas about what constitutes an appropriate match user and product dimensions.
- A suitable percentile has to be chosen.
- If design accommodates people at appropriate extreme of the anthropometric range, less extreme people will get accommodated.
- Re-design or rearrange task to allow employee to sit or to stand whenever necessary for him or her to do so.
- Avoid tasks which require standing in static posture.
- Provide a chair or a stool for sitting on or standing against.
- Provide workstation accessories such as :
- A cushioned surface to stand on (anti-fatigue floor mat).
- Better soles for shoes.
- Adjustable working surface to accommodate differences in employees’ height.
- Small foot bench. (e.g. grating for foot to rest) The best design of any workstation must demonstrate minimal physical stresses to the employees that may lead to localised fatigue, pain and discomforts to the employees.
Berkeley Lab, Public domain, via Wikimedia Commons
Motion Economy
Learning Objectives:
- Define the concept of motion economy and its significance in the context of industrial engineering and workplace design.
- Explain how motion economy focuses on optimizing work methods and processes to minimize unnecessary movements, reduce fatigue, and increase productivity.
- Identify and describe the key principles of motion economy, including the Gilbreth's 17 Principles of Motion, which provide guidelines for efficient work methods.
- Understand the principles related to minimizing unnecessary motions, avoiding excessive fatigue, and improving worker safety.
- The use of human body
- The two hands should initiate and finish their movements simultaneously.
- Aside from rest periods, the two hands shouldn't be inactive at the same moment.
- Motions of the arms should be made simultaneously, in opposite, symmetrical directions.
- Hand and body actions should be limited to the lowest classification that can yet be used to complete the task successfully.
- When possible, momentum should be used to help the worker, and if it must be overcome by muscular effort, it should be minimized.
- Smooth, continuous curving motions of the hands are better to straight, abruptly changing direction motions.
- Arrangement of the work place,
- Each tool and material needs to have a specific location that is fixed in place.
- Equipment, supplies, and controls should be placed close to the use-point.
- Material delivery near to the point of usage should be done using gravity feed bins and containers. When possible, drop deliveries ought to be employed.
- Materials and equipment should be positioned to allow for the ideal series of motions.
- Suitable conditions for viewing should be provided. The first prerequisite for adequate visual perception is good illumination.
- The height of the desk and the chair should ideally be set up to make it simple to switch between sitting and standing while working.
- Design of tools and equipment.
- All tasks that may be performed more profitably by a jig, a fixture, or a foot-operated machine should be taken off the hands.
- Whenever possible, integrate two or more tools.
- When possible, tools and materials should be positioned.
- The burden should be allocated according to the intrinsic capacity of the fingers where each finger performs a specific movement, like while typing.
- The operator should be able to operate levers, hand wheels, and other controls with the least amount of body movement and with the maximum speed and ease.
Solved Example: 9055-01
The principles of motion economy are mostly used while conducting:
A. A method study on an operation
B. A time study on an operation
C. A financial appraisal of an operation
D. A feasibility study of the proposed manufacturing plant.
Correct Answer: A
Solved Example: 9055-02
In micro-motion study, therblig is described by:
A. A symbol
B. An event
C. An activity
D. Standard symbol and colour
Correct Answer: D
Solved Example: 9055-03
What does symbol 'O' imply in work study?
A. Operation
B. Inspection
C. Transport
D. Delay/temporary storage
Correct Answer: A
Solved Example: 9055-04
Micro motion study is:
A. Analysis of a man-work method by using a motion picture camera with a timing device in the field of view
B. Motion study observed on enhanced time intervals
C. Motion study of a sequence of operations conducted systematically
D. Study of man and machine conducted simultaneously
Correct Answer: A
Solved Example: 9055-05
What does symbol 'V' employ in work study:
A. Operation
B. Inspection
C. Delay/ temporary Storage
D. Permanent storage
Correct Answer: D